HL company held final meeting for Lean Audit From July 7th to 9th, the company conducted a semi-annual lean audit in accordance with the "HLPS Promotion Evaluation Guidelines" and held a final meeting on the afternoon of July 9th. General Manager Zheng Wenkui, Deputy General Managers Liu Xingmin, Zhang Baoxin, Wang Jingjun, Liu Gang, and relevant personnel from various departments, and the SDLG lean audit team attended the meeting.
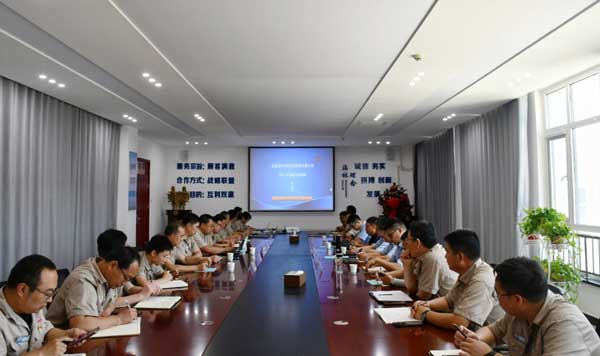
At the meeting, the audit team reported the overall situation of the semi-annual lean audit, affirming the phased achievements and improvement results made by the company in such modules as the implementation of the "HL Way" culture, the effectiveness of cross-departmental team collaboration, the stability of core production processes, and the promotion of the just-in-time production model. After evaluation, the comprehensive score for the middle of 2025 in terms of lean management was 2.32 points.
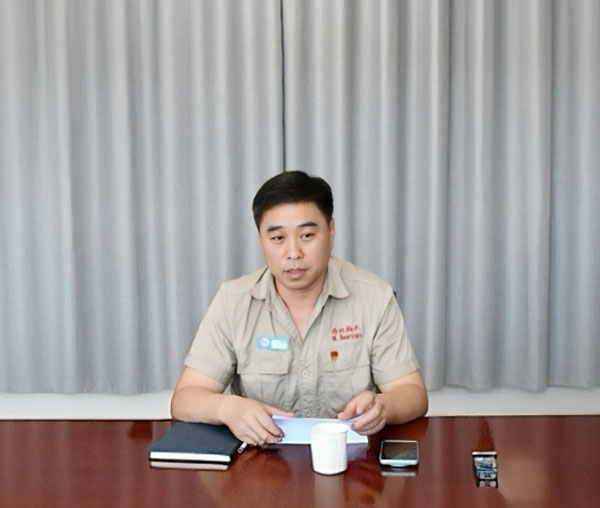
Liu Gang analyzed the lean promotion work at the meeting, emphasizing that module leaders, department "top leaders" and the lean promotion office must earnestly take on their responsibilities, closely cooperate, focus on key points to break through bottlenecks, and ensure the effective implementation of lean management.
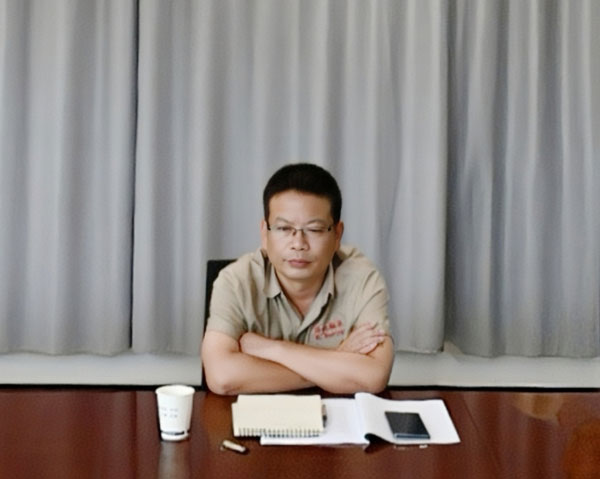
Zhang Baoxin pointed out that the improvement of lean management is essentially a change in behavioral awareness, which needs to break through problems such as passive execution and formalism. He emphasized that the lean management system is an integral whole where all links are interrelated and support each other, and when drawing on experience, attention should be paid to the transformation of substantial effects.
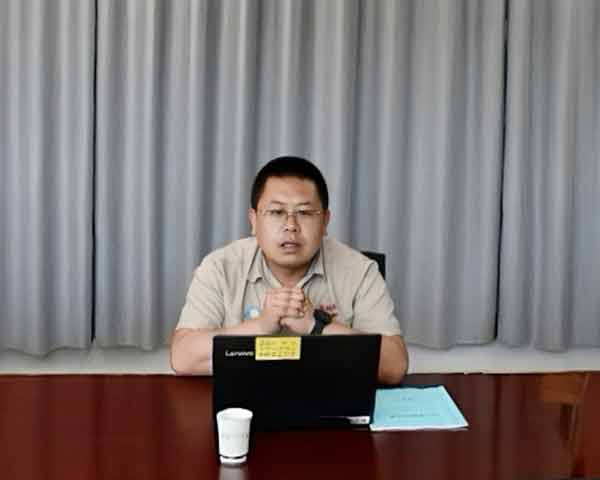
Zheng Wenkui, expressed his gratitude to the SDLG team for their audit guidance. He pointed out that the company has positioned lean management as a long-term strategy and is committed to cultivating it into HL's corporate culture, work philosophy and scientific tool. He required all departments to take this audit as an opportunity to change their perception, promote lean management from "passive coping" to "active value creation", and help improve work quality and efficiency. The company will also make efforts from four dimensions: resource support, expert guidance, supervision and inspection, and assessment incentives to ensure significant progress in lean management work in the second half of the year.